Stretch forming aluminum extrusions is a metal forming process used to shape and contour aluminum extrusions, typically for applications that require complex and curved shapes. Stretch forming aluminum extrusions involves elongating or stretching an aluminum extrusion over a die or a form block, allowing the material to conform to the desired shape without causing significant thinning or material loss. It’s commonly used in industries such as aerospace, automotive, architecture, and more.
Principle
In intension bending, an aluminum profile is clamped on both sides and stretched during the bending process. It is a gentle process that reduces the formation of cracks or pressure points at the bending point.
During stretch forming, an extrusion is placed along a rounded, fixed bending die and clamped in place on each end. The machine begins to swing the clamped ends downward to angles up to 180 degrees, and the extrusion is bent around the die to reach the desired form.
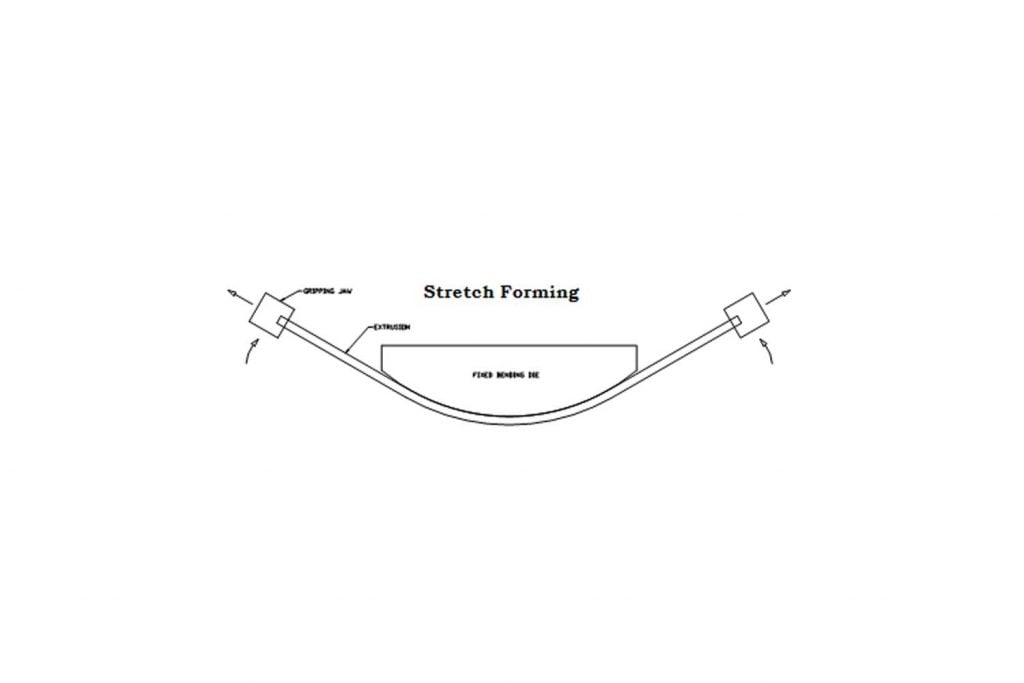
The bend radius is unlimited with this method. A stretch forming machine can bend, twist and lift an extrusion simultaneously to create unique, specified shapes and angles for parts up to 25 feet long. This method also offers the most accurate and consistent bending through elongation control. Because of the way the rounded, fixed bending die pushes on the extrusion, stretch forming has the least amount of surface distortion and traffic marking on the extruded piece.
Stretch forming aluminum extrusions is commonly used for parts with a larger bend radius, as the minimum bend radius is generally two to three times greater than other forming/bending methods.
Top 7 Steps for Stretch Forming Aluminum Extrusions
- Material Selection: High-quality aluminum alloys are commonly used for stretch forming aluminum extrusions due to their malleability and corrosion resistance.
- Die or Form Block Preparation: A die or form block is created, which represents the desired shape of the aluminum extrusion. This form block is often made of steel or other durable materials.
- Clamping: The aluminum extrusion is secured at one end to a clamping device, while the other end is left free.
- Heating (Optional): In some cases, the aluminum extrusion may be heated to increase its ductility, making it easier to stretch and form without cracking.
- Stretching: The clamped end of the extrusion is pulled over the die or form block while the free end is held in place. The stretching process is controlled to ensure uniform deformation.
- Conforming to the Die: As the extrusion is stretched, it conforms to the shape of the die, taking on the desired curvature and contours.
- Cooling (Optional): After forming, the extrusion can be allowed to cool to retain its new shape.
Marjor 5 Advantages For Stretch Forming Aluminum Extrusions
- Complex Shapes: It allows for the creation of complex shapes and contours that may be challenging to achieve with other methods.
- Minimal Material Thinning: Stretch forming minimizes material thinning, preserving the structural integrity of the aluminum extrusion.
- Precise Tolerances: It provides excellent control over dimensional tolerances and surface finish.
- Reduced Tooling Costs: Stretch forming can be a cost-effective alternative to expensive molds or dies, particularly for low-volume production.
- High Repeatable Accuracy: The process can be highly repeatable and suitable for high-precision applications.
Final Words
Stretch forming aluminum extrusions is commonly used in the aerospace industry to create parts like aircraft skins, fuselages, and wing components. It’s also used in architectural applications to create curved metal surfaces. Additionally, the automotive industry may use stretch bending aluminum extrusions for applications like car bumpers and trim components. The process’s versatility makes it a valuable choice for applications that require precision shaping of aluminum extrusions.