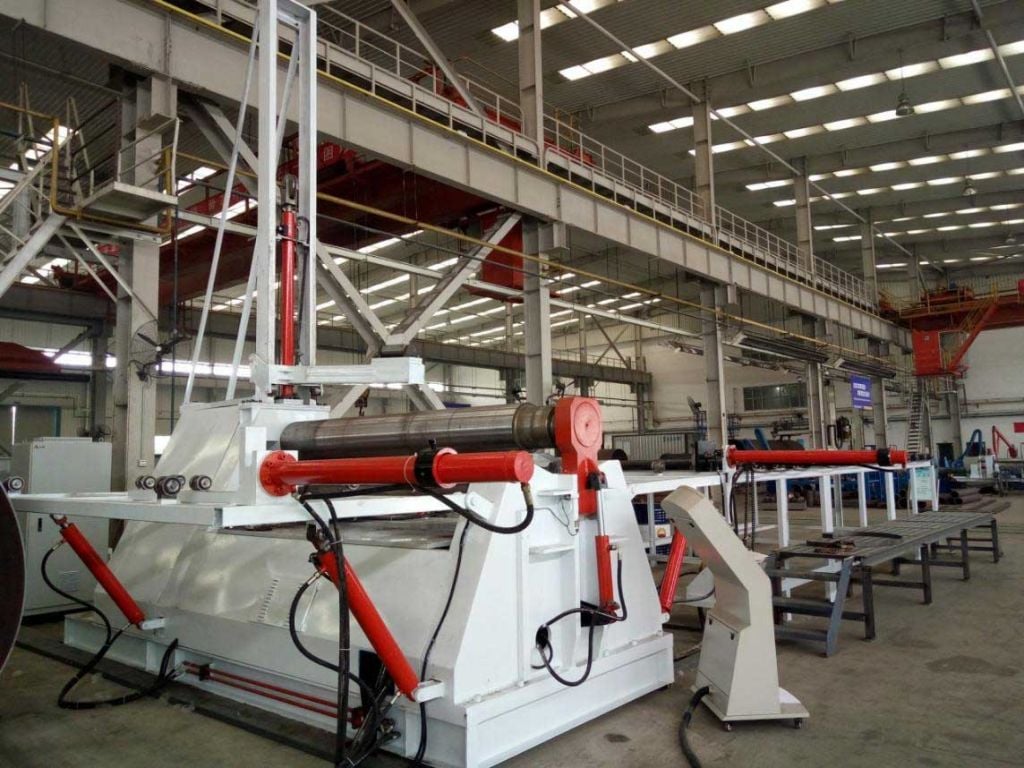
BIT Plate Roll that’s Reliable and Flexible.
CNC Plate Rolling Machine
Enhance Your Plate Rolling Production Efficiency Today, Saving 80% on Labor Costs and Time.
- CNC Automatic 3-Roll Double Pinch, Variable Geometry, and 4-Roll Plate Roller;
- Bending Thickness: 6 up to 350mm; Working Width: 1000 up to 12000mm.
- High-strength and large-torque design; Extra-wide self-aligning bearings; Cooling and heating for the hydraulic system; Transverse and longitudinal corrective top and side supports
High-Quality Plate Roll Manufacturers
Types Of BIT Steel Plate Rolling Machines
PRV Variable Geometry Heavy Duty Plate Rolling Machine
PRV Variable Geometry Heavy Duty Plate Rolling Machine: Plate Rolling Capacity: Bending Thickness: 6-350mm; Working Width: 1000-12000mm.
PRV 3-Roll Bending Machines with the variable geometry design have the function of pre-bending the end of the plate, which can feed the metal plate at one time, and can complete the pre-bending and the plate rolling process.
- Extra-wide series spherical roller bearings;
- Conjoined double hydraulic cylinder drive technology;
- Automatic leveling, synchronization accuracy ±0.2mm;
- Independently adjust the position of the lower roller (cone rolling function);
- 3 rolls are independently driven by hydraulic motors and planetary reducers;
- Cooling and oil-temperature heating devices;
- Radial and axial steel plate alignment function.
PR4 4 Roll Plate Rolling Machine
PR4 4 Roll Plate Rolling Machine: Plate Rolling Capacity: Bending Thickness: 5-280mm; Working Width: 1000-9500mm.
BIT offers a very powerful, hydraulic 4-roll PR4 series plate rolling machine with CNC controls. PR4 is a unique machine for rolling plates with high precision and high-efficiency advanced plate roller equipment.
BIT PR4 series steel heavy plate bending machine has been refined over the years through extensive research and development and is considered one of the finest plate rolling machines available on the market worldwide, which is particularly suited for large sheet metal thicknesses.
- PR4 4 roll bending machines have sufficient rigidity and a long precision retention period.
- The double drive of upper and lower rollers is guided by high-precision linear slide rails and proportional servo valve control.
- Optimized upper roll design: The load factor of the maximum pressure of the upper roll is 0.7.
- Automatic T&F Plate Bending Machine Control Expert System.
- The displacement synchronization accuracy of the upper roller can reach ±0.2mm.
- Independent oil lubrication, accurate oil supply. Can lubricate regularly, at fixed points, and in a quantitative manner during mechanical operation.
4 Other Types of 3 Roll Steel Plate Rolling Machine
BIT also manufactures four other types of high-quality 3 roll bending machines that can be used to roll bending sheet metal and steel heavy plates, Plate Rolling Capacity: Bending Thickness: 20-200mm; Bending Width: 1000-10000mm.
- PRT NC Heavy 3 Roll Plate Rolling Machines
- PRA Initial Pinch Plate Rolling Machines
- PRD Double Pinch 3 Roll Plate Rolling Machines
- PRS Pyramid 3-roll Plate Rolling Machines
Wind Tower Bending Machine
- Thickness specification: 20mm – 240mm, width specification: 3000mm – 4000mm;
- Advanced fully hydraulic variable center distance three-roll mill model;
- High-strength, high-torque design to meet continuous high-intensity work requirements;
- Hydraulic top support, overload overflow;
- With radial and axial correction device side support;
- With centering device power roller way;
- Complete set of accessories to ensure efficient and fast coil rolling.
Ship Plate Bending Machine
- The best model in China embodies advanced European technology.
- It adopts patented technology, with independent power systems driving the two lower rolls, without mechanical interference. The roller bearings are self-aligning roller bearings for rolling mills, with low friction resistance, low energy consumption, and minimal power requirement for the main motor, thus promoting energy conservation and environmental protection.
- Using patented technology, multiple sets of adjustable height support rollers are placed between the upper roll and the upper beam to compensate for the deflection deformation of the upper beam and bed during the coil rolling process, ensuring high rolling precision.
- The synchronous lifting of both ends of the upper roll is automatically controlled by the CNC system, ensuring high synchronization accuracy. The CNC system, independently developed domestically, leads the industry with multiple functions including screen display, rolling calculation, program control, process parameter storage, software protection and fault alarm, human-machine dialogue, and remote control.
- Equipped with corresponding molds, it can perform sheet bending and forming, meeting a variety of user requirements.
Optimize Performance
Now, Plate Rolling Machine that’s precisioner — and efficienter
BIT’s standard 3-roll and 4-roll Plate Rolls are specifically crafted to fulfill the rigorous demands of contemporary metalworking industries. These plate rolling machines from BIT are engineered to deliver efficient and precise bending of metal plate/sheets while offering flexibility to meet diverse bending requirements.
- CNC control, automatic leveling, screen display, synchronization accuracy ±0.2mm.
- Thickness specifications: 6mm—350mm, Width specifications: 1000mm-12000mm
- Designed for high strength and torque to meet continuous high-strength work demands.
- Hydraulic top support with overload overflow.
- Equipped with radial and axial correction devices for lateral support.
- Equipped with a centering device for plate
- A complete set of accessories ensures efficient and rapid plate rolling.
- The fully automatic CNC plate rolling machine control system can automatically calculate and optimize the rolling process, and can automatically complete the pre-bending and rolling work of both ends of the workpiece after loading the material once.
Why Choose BIT’s Plate Rolling Machine?
High-quality parts keep your plate rolls up and running 99.9% of the time.
Expert in Hydraulic Plate Rolling Machines. We Have Over 30+ Years of Manufacturing Experience in Plate Bending/ Rolling Machines: Hot Selling 3, and 4-roll CNC Plate Roll Machines.
Established in 1968, BIT is a Chinese leader in plate-rolling technologies. Our commitment to innovation has positioned us as a driving market force in metal bending technology areas, including profile bending, plate rolling, tube/pipe bending, and aluminum bending equipment.
Structure
- Advanced and reliable structural design for high-precision, high-efficiency metal sheet rolling using unique and advanced equipment.
- BIT’s plate rolling machines possess ample rigidity, with key components like the working roll meticulously selected, expertly manufactured, and exhibiting outstanding performance. They maintain precision for extended periods, suitable for prolonged continuous processing. Their operational control is stable and reliable, offering simple operation.
- The frame, bed, base, and other components undergo three-dimensional finite element analysis, ensuring sufficient strength and rigidity. Post-welding, they undergo annealing treatment to eliminate residual stress.
Working Roller
The working roller is the primary critical component of the plate rolling machine:
- It is made of 42CrMo material, forged using a ten-thousand-ton press, subjected to quenching and tempering treatment, resulting in a hardness range of HB260~300.
- Undergoing triple ultrasonic inspections according to the GB/T6402-2008 standard for third-level non-destructive testing of forged steel components.
- The bearings all utilize heavy-duty self-aligning roller bearings designed for rolling mills, boasting strong load-bearing capacity, minimal friction, extended lifespan, energy-saving characteristics, and meeting the requirements for tilting the working roll.
CNC Control
Expert System for Fully Automatic 3-Roll/4-Roll Bending Machines:
- The human-computer interactive interface of this BIT’s plate roll enables users to input fundamental parameters of the workpiece, such as thickness, width, material, diameter, etc. Autonomously calculates the necessary steps for the plate rolling process. It ensures minimal waste during initial plate rolling.
- Upon completion of the test plate rolling, data is stored for seamless automatic molding.
- BIT’s CNC system ensures full precision and dimensional consistency of the workpiece, making it particularly well-suited for mass production.
Plate Rolling Machine FAQ:
What is plate rolling machine and how does it work?
A plate rolling machine, also known as a plate roll or plate bending machine, stands as a powerhouse within your workshop, offering unparalleled abilities to mold metal sheets. Think of the plate roll as a versatile tool that serves as a master craftsman, shaping metal with precision and finesse. It’s commonly used in various industries like manufacturing, construction, shipbuilding, and metalworking for creating cylinders, cones, pipes, and other curved structures from flat metal sheets.
When your metal sheets are fed into our plate rolling machine, they are carefully positioned between the two, three, or four rollers(2 roll bending machine, 3 roll bending machine, 4 roll bending machine). These rollers work in unison, allowing us to precisely control the metal’s form by adjusting their positions and exerting pressure. It’s similar to a skilled artisan meticulously crafting metal to meet specific design requirements.
Our plate rolling machine ensures your metal sheets adopt a distinct and customized shape, tailored to your precise specifications. Just as a tailor fits clothing to an individual’s measurements, our machine shapes the metal to your exact desires.
For more details about our plate rolls and plate rolling capabilities, we invite you to explore our product information. Should you have any uncertainties about how our machine suits your needs, we encourage comparing its features with those of other leading providers.
Thank you for considering our plate rolling machine service. We are dedicated to delivering superior metal shaping solutions.
Which plate rolling machine is suitable for my workshop?
The plate rolling machine is one of the must-have equipment in the workshop roll shop. You can choose the suitable plate rolling equipment according to your unique metal forming requirements. Plate rolling machines encompass a range of configurations, each suited to specific metal bending requirements, much like varying tools for different tasks.
- 2-Roll Bending Machine: Operates with two rollers, ideal for simpler tasks with uncomplicated curves, suited for basic metal bending needs due to its straightforward functionality and cost-effectiveness.
- 3-Roll Bending Machine: Utilizing three rollers, it grants increased flexibility for shaping metal, accommodating diverse bending demands including moderate curves, cones, and cylinders, suitable for moderately complex metalwork. About 3 roll bending machines we offer 5 solutions: 3 Roll Plate Bending Machine – The Best Buyers Guide
- 4-Roll Bending Machine: Advanced with two bottom and two top rollers, it ensures precise bending without material reversal, offering exceptional accuracy and control for intricate and demanding metal shaping projects. More Detail
Choosing the right plate rolling machine hinges on task intricacy and precision required, ensuring optimal results for specific metal bending needs. You can read the article 3 Types of Plate Rolling Machine Working Principle to know the decision.
What is Heavy Plate Rolling Machine and what are BIT’s benefits?
A Heavy Plate Rolling Machine is a robust industrial machinery designed specifically for bending and shaping thick and heavy metal plates.
- Reliability: For BIT heavy plate rolling machines with heavy plate thicknesses greater than 6 inches, the upper roller main drive adopts a four-hydraulic motor converging structure.
Drives the upper roller to rotate through the hydraulic motor and the planetary reducer gearbox. - Double-cavity cylinder: Standard model, short procurement cycle and stable and reliable quality; long service life of the cylinder and seals. It effectively simplifies the unload side structure, is safe and reliable, and can roll large-taper workpieces.
- Variable Geometry: The PRV variable-geometry plate roll flexibility makes it a suitable choice for medium to thick materials, say more than 1 in. thick.
Variable-geometry plate roll’s two bottom rolls can be positioned under the top roll at just the right spot to leave a minimal unbent flat for the material at hand. - Linear Guided: Linear guided delivers at-par performance and flexibility at much lower costs, therefore ideal for medium-to-heavy duty rolling.
What do you need to prepare before buying a plate rolling machine?
The following parameters need to be provided: the material of the metal plate, such as carbon steel and stainless steel; yield strength; plate width; minimum bending radius; maximum bending radius. Workpiece shape.
- Material Type and Specifications: Determine the materials you’ll be working with, considering aspects like thickness, width, diameter, strength, and yield. These factors dictate the necessary pressure and the maximum and minimum diameter/width for the plate roller.
- Minimum Diameter Requirement: Calculate the minimum diameter required based on the thickest material to be worked upon. The 1.5 rule often applies, where the diameter rolled should be at least 1.5 times the top roll diameter. Understanding this and the material’s yield strength aids in selecting the appropriate plate roll.
- Round vs. Out-of-Round Rolling: Decide if you’ll only be rolling round objects or require special shapes. Utilizing a plate roll with a CNC control facilitates manipulating roll positions and speeds, necessary for shaping non-round objects like ovals or specialized shapes.
- Producing Large Diameters: Assess the size of the diameter you’ll be producing. Larger diameters might necessitate additional support, such as side supports or overhead support, to prevent back bending due to the material’s weight.
Download: Plate Rolling Procedure PDF