BENDING AND ROLL-BENDING THE METAL PROFILE
Difference between bending and roll-bending metal profiles to solve here?
Roll Bending
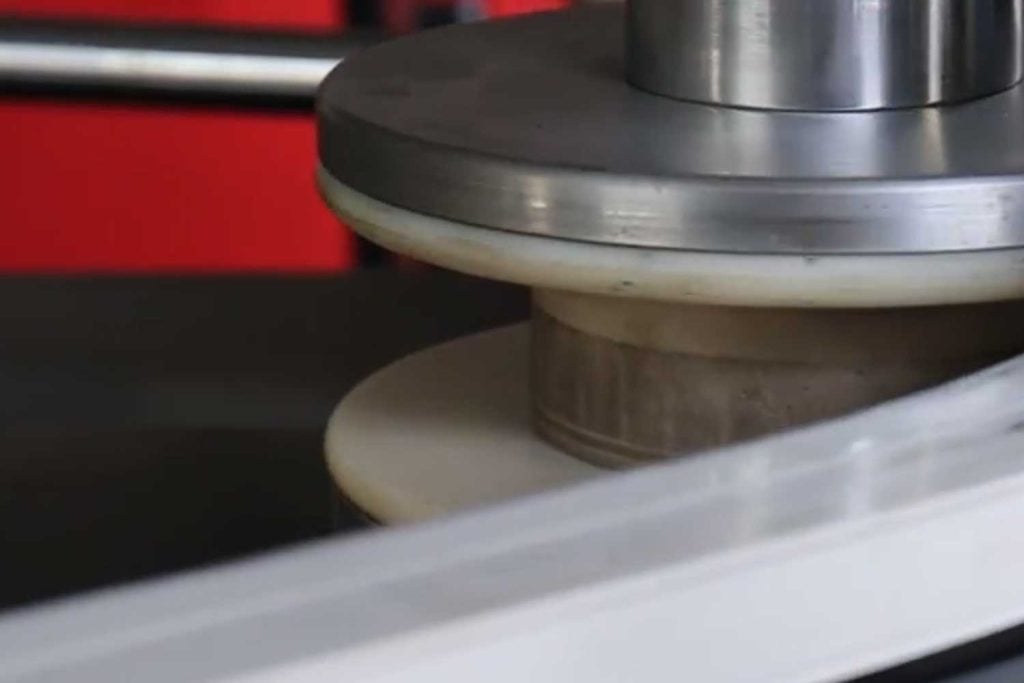
Roll bending is a cold bending process whereby we obtain cold process deformation with a wider bend radius, the metal profile or steel plate is made to pass through a set of three rollers that, will form an arch with the required radius of curvature. Roll bending process in which tubes, steel/aluminum plates, and metal profiles are repeatedly passing it through a set of 3 adjustable rollers resulting in bending progressively, will form an arch or circle with the required radius of curvature. Theoretically, the cold roll bending process can range from 5 times the cross-section to infinity.
A roll bending machine is a mechanical jig having three pressure rollers used to bend a metal profile(tubes/pipes, steel/aluminum plates, metal profiles, H-beams, angle irons, etc) into a circular arc. The pressure rollers freely rotate about three parallel axes, which are arranged with uniform horizontal spacing. Roll bending pushes an extrusion around three different pressure rollers placed in a triangular shape. The pressure rollers are adjusted to form a precise angle, up to a 360-degree rotation, that can roll horizontally or vertically.
Roll Bending Process
The top roller or two lower rollers will be immobile, the lower rollers cradle the bottom of the material while the inner roller(inner roller only in a 4-roll bending machine), whose position is adjustable, presses on the topside of the material. As the material is slowly moved across the power-driven rollers, it begins to curve and bend.
The workpiece is placed on top of the two lower rollers. An upper roll presses the tube down between the two rollers. This causes plastic deformation and bending of the workpiece. The rolls are often shaped to fit the profile shape to prevent deformation of the cross-section.
The metal profile/plate/sheet metal is then fed through the process by the driven rolls and bent in this way continuously.
Extrusions are limited to a single bend per cycle, meaning a higher angle of the bend would take longer to reach the desired angle. Though it may take longer, the maximum bend radius is unlimited. Symmetrical profiles are preferable for roll bending.
Rotary Bending
ELECTRIC ROTARY DRAW BENDING
Electric rotary draw bending uses the same process as the hydraulic method but allows faster setup. The bends also are more accurate and easily repeated because angles and rotations can be automated in a machine’s programmable logic controller. Rotations of the extruded aluminum also can be mechanized for variable plane bends.
Read More: Roll Bending in 12 Metal Bending Processes
The electric rotary draw method is best for applications that require multiple bends per part in close proximity to each other, or different radii bend for each part.
Hydraulic Rotary Draw Bending
In the hydraulic rotary draw bending process, manufacturers place extruded aluminum onto a bender and hold it in place with a stationary or sliding pressure die and clamping block. The round bending dies, powered by hydraulics, is rotated up to 90 degrees, bending the extrusion as it rotates. With this method, an extrusion can only be bent one radius at a time.
Incorporating a mandrel or other tool component to grip the rotary die can prevent creasing or misshaping of the product, though its use isn’t required. The single-axis-controlled revolution can bend within one-tenth of a degree for extremely precise bend angles.
Hydraulic bending is often used when forming round tubes or pipes for applications such as handrails and is ideal for extrusions with a large diameter, such as building signage.
Rotary Bending metal profiles
What does it consist of?
Rotary bending effectively means deforming a section bar, with a relatively narrow radius of curvature.
(That in relation to the diameter of the tube may vary from a minimum of 1.5 times the tube Ø, up to a maximum of 5 times. Metal tubes are bent with special machines called tube benders. )
The metal section profiles are given the shape of the bending die previously installed on the section bending machine.
The most difficult aspect of bending metal tubes is limiting the deformation.
Inevitably, there will be some deformation of any metal tube when it is bent mechanically.
This deformation alters the tube only in the area in which it is bent, particularly in the inner and outer portions of the bend.
Roll Profile Bending
what does it consist of?
Roll-bending is a process whereby we obtain cold process deformation with a wider bend radius that theoretically can range from 5 times the cross-section to infinity. To achieve this process, the equipment used consists of roll-bending machines.
The steel tube is made to pass through a set of three rollers that, after one or more passages (depending on the difficulty of bending), will form an arch with the required radius of curvature. Roll-bending is, generally speaking, a simpler process than bending.
The particular feature of this type of mechanical process is that a single machine can produce different bend radii on the same tube, permitting the creation of complex geometrical shapes.
The disadvantage of roll-bending is the fact that in order to achieve a valid grip and begin the roll-bending process, the machine requires a portion of additional material at the beginning and end of the tube. This necessitates an increase in the total quantity of metal needed to roll and bend the tube
Read More: Profile Bending Machine: 5 Things Before Buy, 6 Steps to Bend
The intrados, shown in red, is a thinner portion of the bend and is subject to compression stresses due to the difference in linear development between the average radius and the inner radius. In the most critical cases, this will cause “crumpling” of the material, shown by the more or less obvious creases in the steel tube.
The yellow part, called extrados, is subject to traction or elongation stress, which results in a thinning of the steel tube caused by bending.
The neutral axis, on the other hand, is a state of absence of stresses, which is not found, in the median portion of the tube but, balancing the tensional status of the piece, usually tends to move into the inner portion of the bend, toward the intrados.
The factors to bear in mind to improve the quality of the bend in a steel tube are:
- The ratio between the average radius of curvature and the diameter/thickness of the tube
- Elongation of the material
- Elastic return
- Esthetics
Rotary Bending
To bend metal profiles, whether of steel or of aluminum, special section bending machines are used. The operation of these machines is mainly electromechanical. Thanks to technological progress, modern section bending machines use FULL ELECTRIC technology, which makes it possible to speed up production and improve the repeatability of bent parts, while at the same time guaranteeing minimum margins of error, even on very high production runs.
What types of steel profiles are suitable for roll-bending?
There are various types of roll-bending machines, capable of bending the widest variety of profiles.
Large sweeping curves, and varying radius curves, such as ellipses, tight bends, rings, and coils, can be achieved for a wide range of sections and material types.
Resource: MP Metal Products
- Bent Tube Profiles; Bent tube is used for numerous applications, from agricultural equipment to roof trusses. Can bent round, square, or rectangular tube in all sizes and materials
- Bent Pipe Profiles: Cold bending process can bend pipe profiles with a diameter of fewer than 20 inches, work with most grades of carbon steel pipe and aluminum pipe, and can create custom profiles from both full and half pipe.
- Bent Bar Profiles: Can create custom-bent profiles from bars in all sizes and shapes: round, half-round, square, hexagonal, and rectangular. It can custom-bend metal bars the “easy way” (on the y-y axis) and the “hard way” (x-x axis) with equal precision.
- Bent Beam Profiles: Can produce custom bent beam profiles in any size, creating even the largest bent beams with superior precision and repeatability.
- Bent Channel Profiles: Bent channels with flanges out, flanges in, or “the hard way.”
- Bent Tee Profiles: Bent tee profiles “stem in,” “stem out,” or “stem up,” with minimal distortion.
- Bent Angle Iron Profiles: Custom-bent angle profiles in nine orientations with minimal distortion.
- Bent Steel Section Profiles: Complete section bending services, custom-bent profiles from standard mill shapes, extrusions, and more.
- Custom Profiles from Rolled Plate: Accurately roll steel and aluminum plates into full cylinders, full cones, and cylinder cone segments, as designs require.
To rotary-bend or roll-bend?
- The main difference between rotary bending and roll-bending is the radius of curvature – narrow or wide – of the tube.
- The second difference is that roll-bending is the only technique that can be used to bend the same metal tube with different bend ratios.
In this sense, we also speak of variable bend radius.
To have a more precise idea of what the maximum bend radius is, we have to multiply the tube diameter by five. If, for example, the tube diameter is Ø50 mm., the minimum roll-bending radius is 250 mm. To obtain a smaller bend radius it will be necessary to bend the tube with a CNC tube bender.
The minimum bend radius is calculated with a special formula that gives us a coefficient; if the coefficient exceeds a certain value it determines the feasibility of bending for a specific radius.
In bending steel, the use of special equipment contributes to the quality of the bent profiles, above all in those cases in which the aforementioned coefficient is at the limit of feasibility.