To determine if a steel section can be curved you need to first determine its section modulus and then see if you have the correct bending equipment.
Section modulus VS elastic section modulus
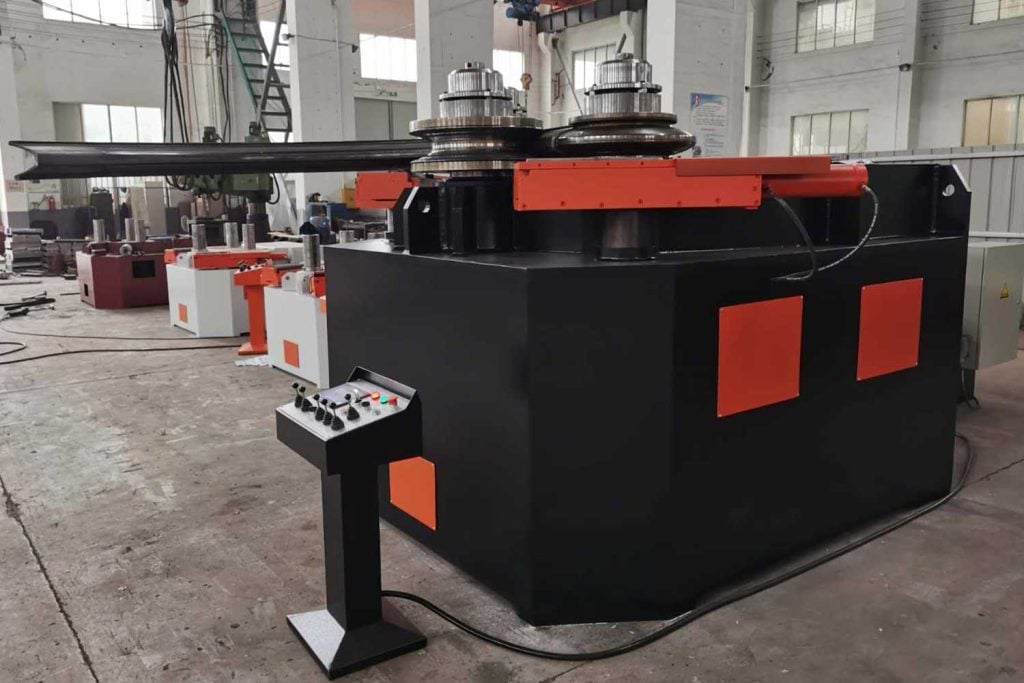
Section modulus is the direct measure of the strength of the steel. Bending a steel section that has a larger section modulus than another will be stronger and harder to bend. Section modulus is a geometric property for a given cross-section used in the design of flexural members.
There are two types of section moduli, the elastic section modulus (S) and the plastic section modulus (Z).
Section modulus (Z)
Another property used in beam design is section modulus (Z).
The section modulus of the cross-sectional shape is of significant importance in designing beams. It is a direct measure of the strength of the beam. A beam that has a larger section modulus than another will be stronger and capable of supporting greater loads.
It includes the idea that most of the work in bending is being done by the extreme fibres of the beam, ie the top and bottom fibres of the section. The distance of the fibres from top to bottom is therefore built into the calculation.
The elastic modulus is denoted by Z. To calculate Z, the distance (y) to the extreme fibres from the centroid (or neutral axis) must be found as that is where the maximum stress could cause failure.
Effective Elastic Section Modulus
The section modulus of any component will be the ratio of second moment area of the section considered divided by the distance of its center of gravity from the neutral axis. It is an important property considered in analysis of flexural strength and moment resistance in case of beams. The second moment of area is taken about the axis of bending.
Section modulus can be of two types:-elastic and plastic section modulus.
Elastic section modulus is the value of modulus taken within the elastic limit, while the plastic section modulus is beyond the elastic limit.
The maximum load that a member can withstand is determined from the effective area of the member directly in contact with the load. Shape and size of a particular member also influences the type of load that it can withstand and the critical load factor for the failure. The stiffness is an important property of the material, which is directly proportional to the elasticity modulus along with moment of inertia. Hence, the effective elastic section modulus can be controlled by varying the effective shape of the material to influence the stiffness of that material.
Elastic section modulus is also critical for determining the moment of resistance, offered by a beam before reaching failure. Effective section modulus of circle and diamond shape components can be increased by removing a thin section at the top.
What’s the difference between plastic section modulus and elastic section modulus?
- The plastic section modulus assumes the entire section yields.
- Elastic modulus is the steel modulus based on the stress strain curve before yielding.
- The plastic modulus is after yielding.
The main difference between elastic modulus and section modulus is that, elastic modulus is the property of a material. (ie: elastic modulus will be different for different materials like steel, aluminum etc. It doesn’t depends on the shape of material).
But section modulus is the property of a cross section of the structure or beam or column. That means that for identical crossection section modulus will be same irrespective of there materials.
So if we make two beams of identical crossection but of different materials then there section modulus will be same because it depends only on the dimensions of crossection, but the elastic modulus will be different for both shafts as they are made of different materials and elastic modulus is a property of material.
Now if we talk about the formula then:
Elastic modulus or modulus of elasticity =stress/strain
Section modulus = (second moment of area) /(distance of outer most point of section from neutral axis)
Section modulus with section bending processes
In the case for bending a steel section it is important to calculate ‘S’ by taking the moment of inertia of the area of the cross section of a structural member – divided by the distance from the neutral axis to the furthest point of the steel section. This is where the steel will bend first. The bending moment that it takes to yield that section equals the section modulus times the yield strength.
In simple terms, the section modulus is the ratio of bending moment to bending stress for steel. If your steel has a high section modulus it will be harder to bend and can withstand a high moment without having high bending stress. You need to divide the maximum bending moment by the section modulus to get the bending stress and then compare the bending stress to the allowable tensile stress to see if the steel can take that much moment. All bending equipment have section modulus ratings.
How to determine
A three-roll section bending machine (section rollers) can be designed to bend steel with section modulus between 0.4 to 500 in3. So, to determine if the section bending machine can bend your steel section, you need to calculate the section modulus mathematically or by referring to engineering tables.
Then, if that amount is equal or less than that of the calculated strength of the section rollers, your angle rolls should be able to curve the section.